Understanding Plastics Injection Molding: A Comprehensive Guide
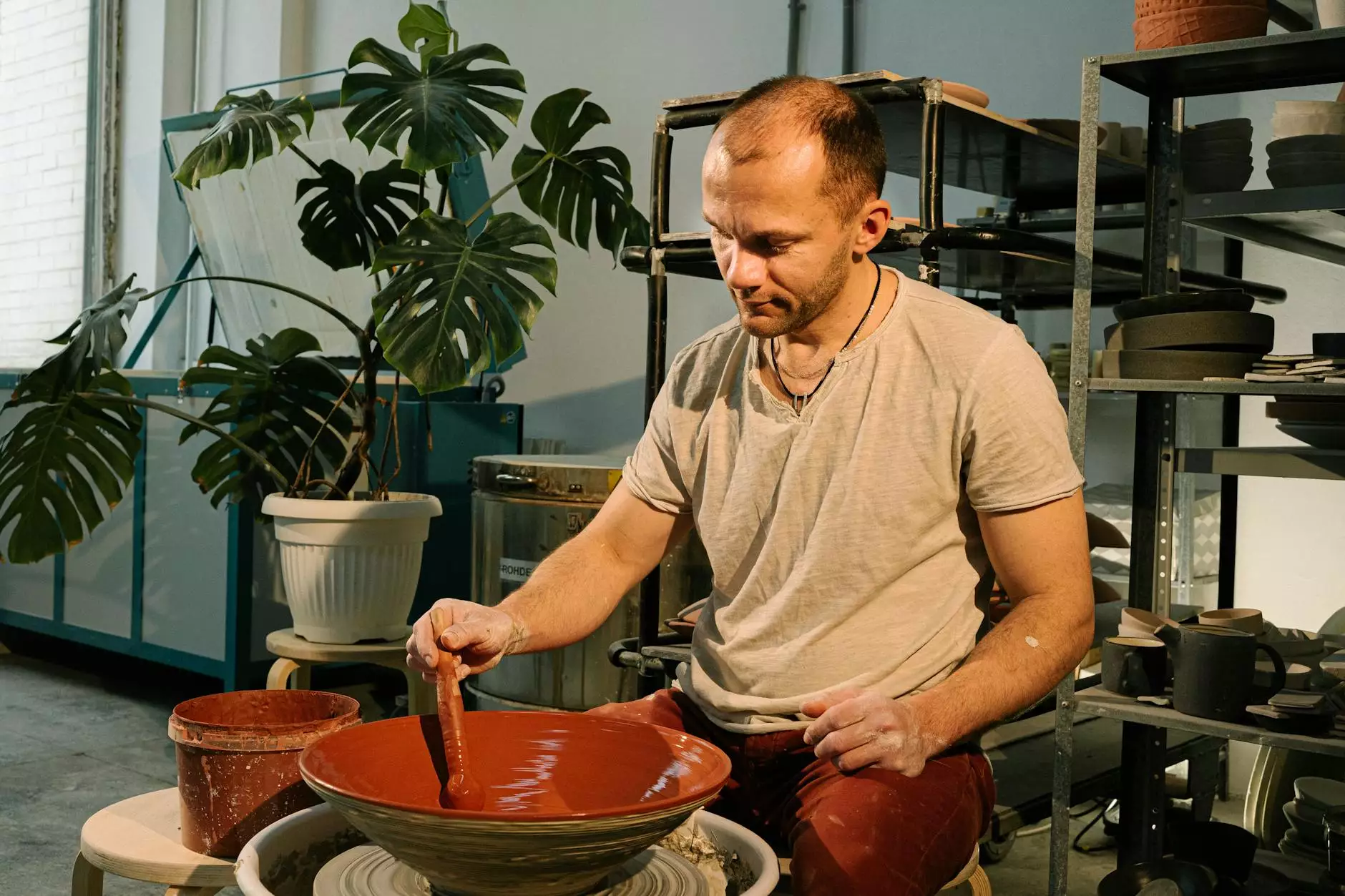
Plastics injection molding is a revolutionary manufacturing process that has transformed industries by providing an efficient and effective way to produce plastic parts. In this article, we will delve deeply into the intricacies of this technology, explore its various applications, and highlight its significance in contemporary manufacturing environments.
What is Plastics Injection Molding?
At its core, plastics injection molding involves the process of melting plastic and injecting it into a mold. This process allows for the creation of complex shapes and designs that would be difficult or impossible to achieve with traditional manufacturing methods. The use of molds enables manufacturers to reproduce parts with high precision and consistency, making plastics injection molding a favored choice across various sectors.
The Process of Plastics Injection Molding
The plastics injection molding process can be broken down into several key stages:
- Material Selection: Commonly used materials include thermoplastics like ABS, polycarbonate, and polypropylene.
- Melting the Plastic: Plastic pellets are heated to their melting point in an injection molding machine.
- Injection: The molten plastic is injected into a mold under high pressure.
- Cooling: The plastic cools and solidifies in the mold, acquiring its final shape.
- Demolding: Once cooled, the mold opens, and the finished product is ejected.
Benefits of Plastics Injection Molding
Understanding the benefits of plastics injection molding helps businesses decide whether it’s the right manufacturing method for their needs. Here are some key advantages:
1. Efficiency and Speed
One of the most significant advantages of plastics injection molding is its rapid production capability. Once the mold is created, which can be costly in itself, the process of producing each individual part is extremely fast—often measured in seconds.
2. Precision and Quality
With precise control over the injection process and the ability to create intricate designs, manufacturers often find that products made with this method exhibit a high level of quality and consistency.
3. Reducing Waste
Unlike other manufacturing processes that may result in excess material, plastics injection molding is highly efficient, allowing for minimal waste of raw materials. This sustainability aspect is increasingly vital in our environmentally-conscious society.
4. Flexibility in Design
Injection molding opens up avenues for creative and complex designs without significantly increasing production costs. This flexibility can lead to innovative products.
5. Cost-Effectiveness for High Volume Production
While initial mold creation can be expensive, the cost per part decreases significantly when producing large volumes. This makes plastics injection molding a cost-effective solution for large-scale manufacturing operations.
Applications of Plastics Injection Molding
The applications of plastics injection molding are vast and varied. Here are some key industries where this technique plays a crucial role:
- Automotive Industry: Used for producing dashboard components, panels, and numerous other parts.
- Consumer Goods: Many household items, toys, and packaging solutions are made through injection molding.
- Medical Devices: Critical applications in manufacturing syringes, surgical instruments, and other medical tools.
- Electronics: Production of casings and components that are lightweight yet durable.
- Industrial Equipment: Used for creating durable parts such as handles, housings, and connectors.
Understanding the Different Types of Plastics Used
There are several types of plastics that can be utilized in plastics injection molding. The choice of material affects the performance and cost of the final product. Some notable types include:
- Thermoplastics: These materials can be remolded multiple times and are ideal for a variety of applications.
- Thermosetting Plastics: Once set, these plastics cannot be remolded, making them suitable for high-heat applications.
- Elastomers: Flexible materials often used in medical and consumer products.
The Role of Technology in Enhancing Injection Molding
Modern advancements in technology have significantly enhanced the plastics injection molding process. Some key developments include:
- The Use of CAD/CAM: Computer-aided design and manufacturing tools aid in precise mold design and production.
- 3D Printing: As a complement to injection molding, 3D printing can create molds or prototypes quickly, speeding up the overall process.
- Advanced Robotics: Automation in the injection molding process enhances efficiency and minimizes human error.
Choosing the Right Injection Molding Manufacturer
When looking to implement plastics injection molding for your business, selecting the appropriate manufacturer is critical. Here are some factors to consider:
- Experience and Expertise: Look for a manufacturer with proven experience in your desired industry.
- Technology and Equipment: Ensure that the company uses modern technology to optimize the molding process.
- Customer Support: A responsive and supportive manufacturer can significantly enhance your experience and satisfaction.
- Quality Assurance: Verify that the manufacturer has quality control systems in place to ensure that products meet regulatory standards.
The Future of Plastics Injection Molding
The future of plastics injection molding looks promising. With ongoing advancements in materials science, automation, and sustainability practices, the industry is poised for significant growth and innovation. The demand for custom plastic solutions across various sectors continues to rise, pushing manufacturers to adapt and innovate.
Incorporating Sustainability
As businesses become increasingly conscious of their environmental footprint, many are seeking sustainable practices in production. Incorporating recycled materials into the injection molding process or developing biodegradable plastics can significantly enhance the sustainability quotient of this manufacturing method.
Embracing Smart Manufacturing
The rise of the Internet of Things (IoT) and smart factories will also influence plastics injection molding. By leveraging data and analytics, manufacturers can enhance productivity, reduce downtime, and improve product quality.
Conclusion
Plastics injection molding remains a cornerstone of modern manufacturing, providing solutions that combine speed, efficiency, quality, and flexibility. Its wide range of applications across multiple industries underscores its significance in today’s economy. As technology continues to evolve, businesses that leverage this powerful process will undoubtedly lead the charge in innovation and competitive advantage.
Whether you’re a small business or a large corporation, understanding the intricacies of plastics injection molding can help you make informed decisions that positively impact your production processes and product quality.
For more information about our services, feel free to contact us at deepmould.net.