The Low Pressure Casting Process: A Game Changer in Manufacturing
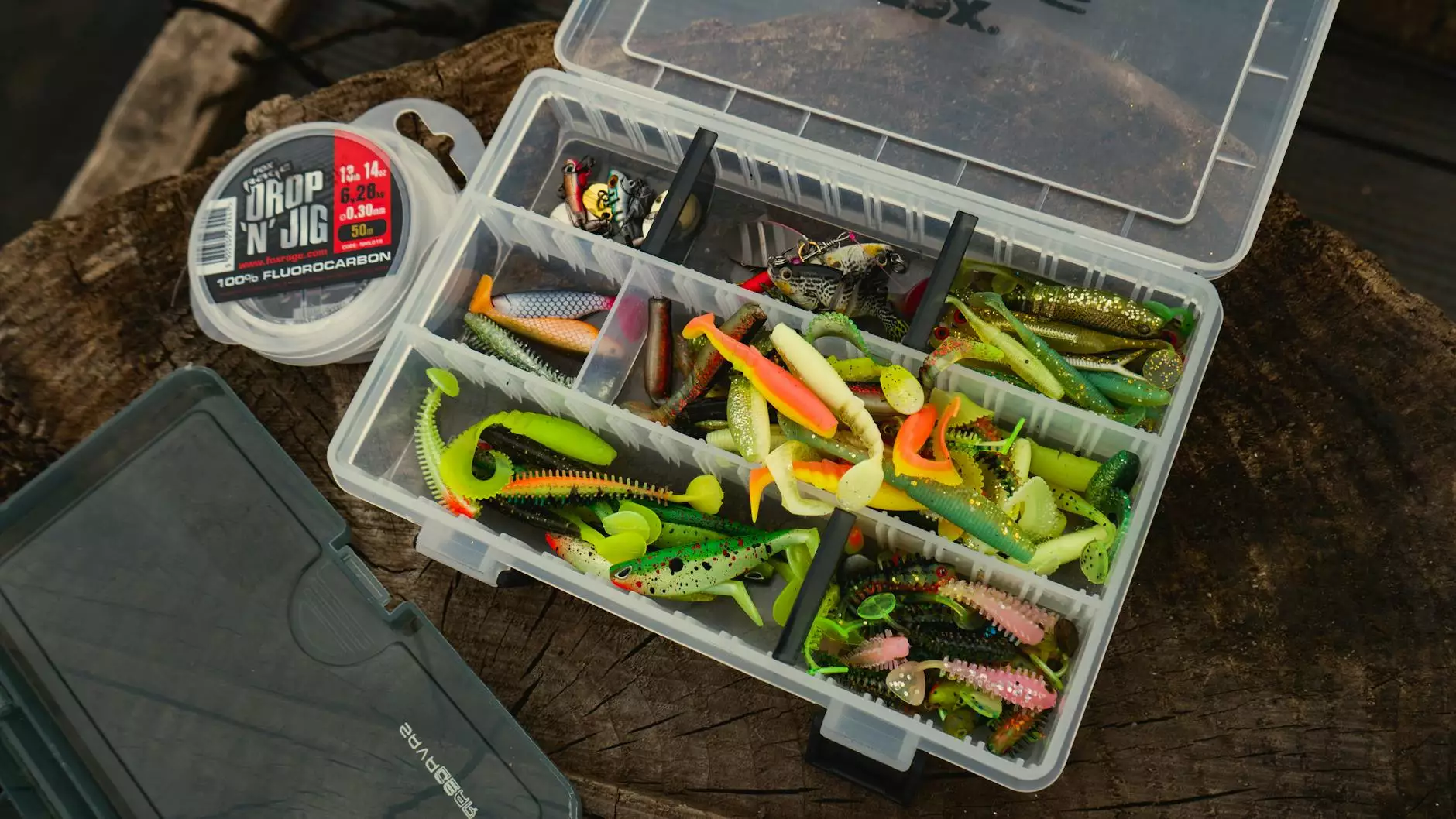
In the realm of manufacturing, efficiency and precision are paramount. One method that has been making waves in achieving this is the low pressure casting process. This technology is not just redefining the way we approach casting; it is pioneering advancements across various sectors including art supplies, product design, and 3D printing. With its ability to produce high-quality castings with intricate details, the low pressure casting process stands out as a superior choice for many manufacturers.
Understanding the Low Pressure Casting Process
The low pressure casting process involves injecting molten metal into a mold under low pressure, often ranging between 0.5 to 2 bars. This method differs significantly from traditional sand casting or gravity casting techniques, which rely solely on gravitational force. The low pressure technique offers several advantages that make it a preferred choice in various industries.
Key Components of Low Pressure Casting
- Mold: Typically made from materials like metal or sand, designed to withstand high temperatures.
- Furnace: Used to melt the metal, ensuring it's at the right temperature for flow.
- Injection System: A crucial element that helps in the controlled injection of molten metal into the mold.
- Cooling System: Ensures uniform cooling of the cast products.
Advantages of the Low Pressure Casting Process
Employing the low pressure casting process offers numerous advantages that can significantly enhance production quality and efficiency:
1. Enhanced Quality and Precision
The low pressure method provides excellent control over the flow of molten metal, resulting in fewer defects and higher precision compared to traditional casting methods. This is particularly beneficial in product design, where detail and quality are essential.
2. Reduced Waste and Material Efficiency
One of the standout features of the low pressure casting process is its efficient use of materials. The technique minimizes waste, allowing manufacturers to utilize more of the raw materials, hence reducing costs and environmental impact.
3. Complex Geometries Made Possible
With the ability to fill molds rapidly and uniformly, the low pressure casting allows for the creation of complex shapes that were previously difficult to achieve. This capability is invaluable in industries that demand high-quality visual aesthetics, such as art supplies and consumer products.
4. Faster Production Times
Speed is crucial in today's fast-paced manufacturing environment. The low pressure casting process allows for quicker cycles and shorter lead times, making it an ideal choice for companies looking to reduce time-to-market.
Applications of Low Pressure Casting
The applications of the low pressure casting process are vast and varied. Here are some of the most significant fields where this technique is revolutionizing production:
1. Automotive Industry
The automotive sector relies heavily on the low pressure casting process for producing components such as engine blocks, transmission housings, and other critical parts. The precision and durability offered by this process ensure that these components can withstand the rigorous demands of vehicle operation.
2. Aerospace Engineering
Aerospace applications require components that are not only lightweight but also capable of handling extreme conditions. Low pressure casting meets these demands, allowing manufacturers to create high-strength, lightweight components that are essential for flight safety and performance.
3. Electronics
Many electronic devices require intricate metal components. The low pressure casting process facilitates the production of high-precision parts that optimize the functionality and durability of electronic devices.
4. Art Supplies and Sculpture
In the realm of art supplies, artists and manufacturers benefit from low pressure casting through the production of high-quality sculptures and decorative pieces. The ability to create complex designs with smooth finishes enables artists to push the boundaries of their creativity.
5. Medical Devices
In the medical field, where precision is non-negotiable, low pressure casting facilitates the manufacture of intricate medical devices and components with exceptional reliability and accuracy.
How Low Pressure Casting Compares to Other Methods
To appreciate the advantages of the low pressure casting process, it is essential to compare it with other casting methods like traditional gravity casting, pressure die casting, and sand casting.
1. Gravity Casting
Gravity casting relies entirely on gravitational forces to fill molds, which can lead to air gaps and defects in more complex designs. In contrast, low pressure casting uses controlled pressure to ensure that molten metal flows uniformly, leading to better surface finishes and structural integrity.
2. Pressure Die Casting
While pressure die casting offers similar benefits in terms of precision, it often requires higher pressures and is more suited to high-volume production. Low pressure casting, on the other hand, offers flexibility, making it an excellent choice for both low and high volume runs.
3. Sand Casting
Sand casting is a traditional method that, while cost-effective for simple shapes, often cannot match the detail and integrity provided by low pressure casting due to its slower cooling rates and potential for sand inclusions. This limits its application in high-precision environments.
Future of Low Pressure Casting
The future of the low pressure casting process looks promising, with ongoing innovations that are set to enhance its capabilities.
1. Technological Advancements
As technology evolves, so too do the machines and techniques used in low pressure casting. The integration of automation and artificial intelligence can streamline processes, improve quality control, and further reduce costs.
2. Sustainable Practices
With an increasing focus on sustainability, developments in low pressure casting are aimed at reducing energy consumption and environmental impact, making this process an even more viable choice for eco-conscious manufacturers.
3. Customization and On-Demand Production
The demand for customized products is rising. The flexibility that low pressure casting offers allows for on-demand production, which can be tailored to specific customer needs, thus enhancing customer satisfaction.
Conclusion
In conclusion, the low pressure casting process is revolutionizing the manufacturing landscape. With its enhanced quality, efficiency, and ability to create complex geometries, it has become a preferred method in numerous industries, from automotive to art supplies. As technological advancements continue to shape this process, it is clear that low pressure casting will play a significant role in the future of manufacturing.
For businesses like arti90.com, which focus on art supplies, product design, and 3D printing, adopting low pressure casting technology can significantly enhance product offerings, meet rising quality standards, and provide competitive advantages in an ever-evolving market. Embracing this innovative casting technique not only positions companies favorably within their industries but also opens the door to endless creative possibilities.